PPH groove adopts the processing technology of one-time extrusion, winding and hot melting. Compared with the original processing technology of PP plate, it eliminates the multi seam seam and seam, thus eliminating the aging and leakage of materials. The mechanical strength, safety and reliability, and comprehensive performance are greatly improved.
The maintenance cycle of PPH tank is generally 60-120 days for medium maintenance and 12 months for overhaul. Medium repair: eliminate running, emitting, dripping and leaking. Clean or replace the level gauge, repair or replace the inlet, outlet and blowdown valves, dredge and clean the cooling water coil. Check and repair the relief valve vent flame arrester. Repair anti-corrosion coating and thermal insulation layer. Overhaul: including the repair of groove internals in the medium repair project, and the corresponding repair or replacement of the cylinder section in case of cracks, serious corrosion and other parts. Polymer composite materials can be used for repair. Leakage test or hydraulic test shall be carried out according to internal and external inspection requirements and after repair or replacement of cylinder joint. All aspects of embroidery removal and insulation. Handle other problems found in the internal and external inspection of the PPH slot. Maintenance methods and quality standards For the repair of PPH slot, such as opening, repair welding, replacement of cylinder section, etc., a specific construction scheme shall be formulated according to relevant standards and specifications.
The current PPH tank series products not only meet the process requirements of lithium battery material production process such as storage, mixing and reaction, but also meet the image demands of energy conservation and environmental protection in the new energy field, and make contributions to cost saving and efficiency increase of enterprises. PPH mixing tank
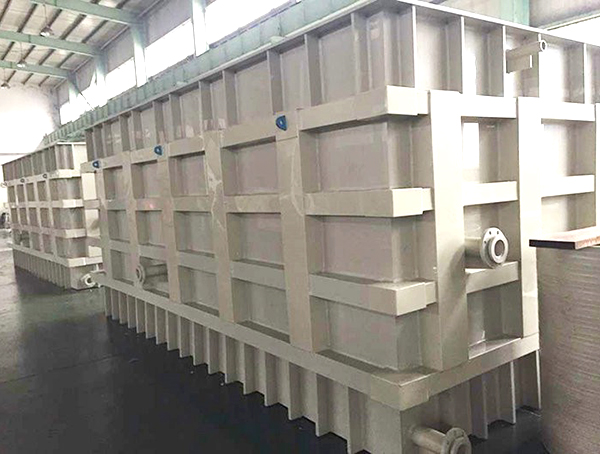