Sansha PPH Reactor Company
PPH winding tank is a plastic tank with good development prospects at present. Its advantage is that the change of processing technology makes it outstanding in the tank. PPH storage tank body uses PPH particulate raw materials to melt with a screw extruder, and then the molten extrusion raw materials produce the tank body on the grinding tool. After a certain level of temperature is reduced, the molding can ensure the integrity of the tank body. Internal welding process features: high mechanization and automation, and stable product quality. The weld specifications can be designed according to the stress characteristics of the product, so as to give full play to the integrity of the weld. The product has good integrity, the weld is integrated with the parent body, and has good corrosion resistance and leakage resistance. It can reduce flash, and the joints are smooth and beautiful. UV absorber is added to PPH granules to prevent aging and prolong service life.
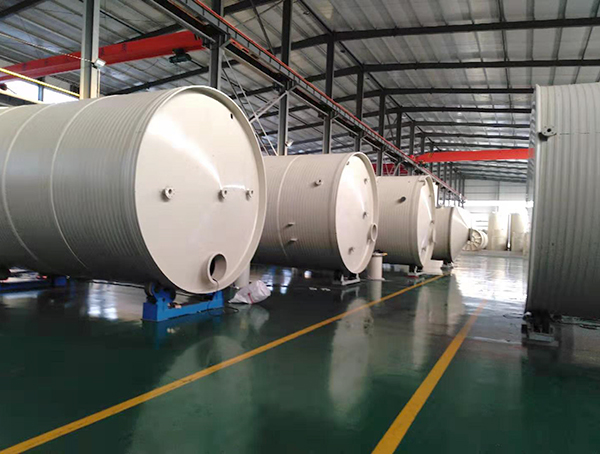
Sansha PPH Reactor Company
PPH storage tank has good temperature resistance, acid and alkali resistance, high strength and impact resistance, longer service life, and no environmental stress fracture damage. At present, the tank has become a necessary equipment for chemical industry, smelting, rare earth, mining, pigment, printing and dyeing, new materials, new energy, and biomedicine. In the next few years, PPH storage tanks will be widely used. Manufacturing process of PPH storage tank: extruding and winding PPH granular materials. The product is formed at one time without welding. PPH tank is welded by polypropylene plate. In terms of corrosion resistance, PPH vertical storage tank and PH vertical storage tank have similar corrosion resistance. From the perspective of safety performance, the PPH tank shell is integrally formed without welding and leakage, while the PPH tank is welded, which is easy to cause leakage and increase unsafe factors. There is a big gap between the other two properties, such as aging resistance.
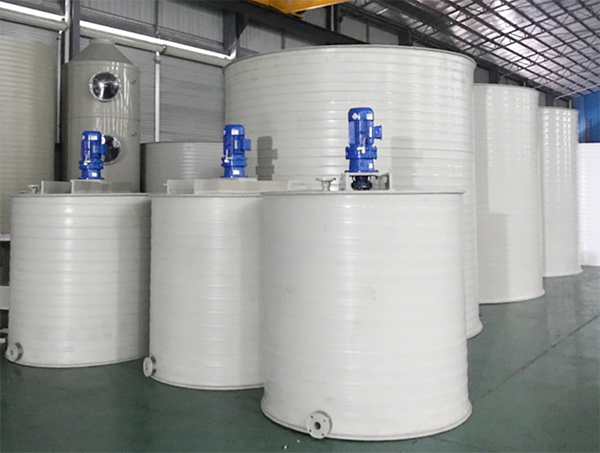
Sansha PPH Reactor Company
The thickness requirements for the bottom plate and top plate of PPH storage tank, the previous welding process is to use a portable welding gun to melt the welding rod, and then weld the tank body and bottom plate together. Since the welding rod is an external accessory, it cannot guarantee the consistency of the material with the bottom plate and tank body, which has a certain impact on the quality of equipment. Using a portable welding gun to weld, it cannot achieve the same welding strength, and the weld surface is uneven, There are many hidden dangers for equipment leakage. The bottom plate and can body are welded by mechanical welding process, which can be divided into external welding and internal welding. The external welding of PPH storage tank is a process that uses the imported automatic extrusion welding unit to realize the one-time welding molding of large welds at the stressed parts of the storage tank. The new PPH granular material with the same property as the tank body is hot melted at the large weld seam, and is integrated with the tank bottom and tank body. Internal welding is an automatic long arm extrusion welding process, which is an important step in all processes. Its principle is the same as external welding, but its equipment is different.

Sansha PPH Reactor Company
Why can PPH storage tank replace stainless steel? The comparison of two kinds of dangerous chemical storage tanks is made from the aspects of mechanical strength, service life, corrosion parameters, maintenance, service temperature, etc. The service life of PPH storage tank is usually 8-10 years, while that of stainless steel storage tank is 10-13 years more; The mechanical strength of stainless steel storage tank is higher than that of PPH storage tank, but hazardous chemicals storage tank is generally placed statically, instead of storage tank with high mechanical strength; PPH storage tank is resistant to most acids, alkalis, organics and mixed liquids. As long as the service temperature is within the limited range, there will be no corrosion. Many media that PPH storage tank can resist will corrode stainless steel (except special stainless steel); In terms of maintenance, PPH storage tank is simple in maintenance and tools, which can be handled by the manufacturer; The service temperature of dangerous chemicals is generally normal temperature, and the high service temperature of PPH storage tank z can reach 100 ℃.

Sansha PPH Reactor Company
PPH mixing tank is made by seamless extrusion winding technology. Pipe orifice, inner weld and outer weld are all processed by automatic extrusion unit equipment, which is superior, stronger and lower than plastic tanks made by traditional technology. It is necessary to use electric heating to melt and extrude the particles onto the steel mold, which consumes a lot of power. The PP storage tank only has the power of the welding gun, so it consumes less power; The PPH mixing tank is welded with a large extrusion electric heating drag gun, which consumes a lot of power. The PP storage tank uses a small manual drag gun, which consumes less power. PPH reaction kettle uses PPH spiral extrusion and winding unit to process PPH granules into tank body forming process. The system adopts the process of hot melting PPH particles, extruding them, and then winding them onto steel dies to form cans. PPH reaction kettle has the characteristics of good integrity, uniform thickness, corrosion resistance, seamless, aging resistance and good leakage resistance.

Sansha PPH Reactor Company
PPH waste gas treatment tower is generally divided into cylindrical tower body or square tower body. The cylindrical tower body is generally vertical tower, and the square tower body is generally horizontal tower. There are multi-stage packing rings inside. During operation, the waste gas flows upward from the bottom of the tower. Due to tangential entry into the tower, especially the guiding effect of the packing layer, the flue gas rotates and rises, resulting in full contact between the packing layer and the waste gas, which sprays the downstream liquid into droplets, leaving a large contact area between gas and liquid; The liquid droplets will also be driven by the air flow to rotate, and the centrifugal force generated will strengthen the air contact at night. They will fall onto the tower wall and flow down along the wall, passing through the overflow device to the next layer of packing, and then the spray nozzle will atomize again for gas-liquid contact.