Lincang PPH storage tank installation
In the use of PPH storage tank, the process of reaction material mainly depends on the change of storage tank temperature to realize the reaction. When designing PPH storage tank, its pressure and temperature should be standardized. The pressure here refers to the gauge pressure unless otherwise specified. Working pressure refers to the possible high pressure at the top of the container during normal operation. Design pressure: the pressure used to determine the shell thickness at the corresponding design temperature. 1.05 times the high working pressure shall be taken for the internal pressure vessel, and the static pressure of the liquid shall be included. The design pressure of external pressure vessel shall not be less than the possible large internal and external pressure difference under normal operation; Test pressure: refers to the pressure at the top of the vessel under pressure test; The vacuum vessel is designed according to the external pressure. When a safety control device (such as a vacuum relief valve) is installed, the design pressure is taken as the smaller value of 1.25 times the internal and external pressure difference or 0.1MPa, or 0.1MPa if there is no safety control device.

Lincang PPH storage tank installation
PPH storage tank is more advanced in materials and processing technology than polypropylene storage tank, but this will not lead to the price of the former being significantly higher than the latter, which is mainly due to the removal of intermediate profits and labor saving in the intermediate plate link. The whole tank body is thin and thick, so that the whole cylinder body is evenly stressed, the design is reasonable, and the mechanical strength and safety reliability of the tank body are guaranteed. In addition to being able to safely fill various corrosive liquids and having good sealing performance, the tank is light in weight and clean in appearance, and has more reliable advantages than plastic roll forming technology, plastic plate welding, FRP roll, hand glue technology, carbon steel lining technology and other technologies. The welding of the bottom of the tank and the bottom of the tank is the part that bears the large stress z. The internal and bottom of the tank are welded by mechanical cantilever, which can realize the large welding once without repeated welding, ensure that the tank and the tank will not leak under the rh condition, and can safely withstand various corrosive liquid operations.
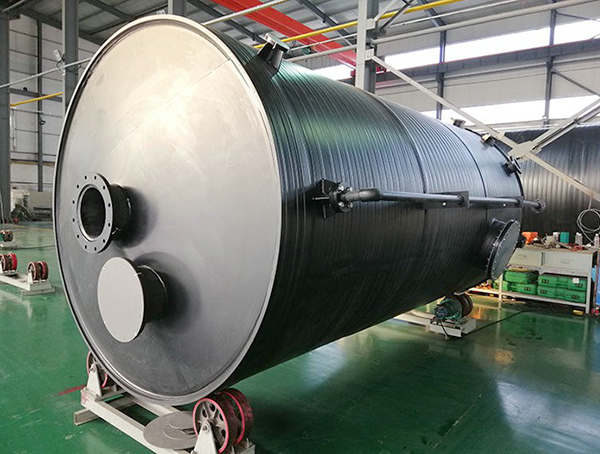
Lincang PPH storage tank installation
Comparison of PPH mixing tank price and PP mixing tank and maintenance measures. It is necessary to use electric heating to melt and extrude the particles onto the steel mold, which consumes a lot of power. The PP storage tank only has the power of the welding gun, so it consumes less power; The raw material of PPH mixing tank is PPH granular material, and the raw material of PP storage tank is polypropylene plate. The price of PPH granular material is more expensive than polypropylene plate; Cooling and demoulding are required, which are performed by electric device, but not for PP storage tank; Steel molds are required for processing, and natural gas is required for preheating before processing. The startup cost is high, and PP storage tank is directly rolled into a tank with polypropylene plates, so the cost is low; The PPH mixing tank is welded with a large extrusion electric heating drag gun, which consumes a lot of power. The PP storage tank uses a small manual drag gun, which consumes less power.

Lincang PPH storage tank installation
The working principle of PPH waste gas tower is to separate the pollutants in the gas and convert them into harmless substances to purify the gas. It belongs to differential contact countercurrent type. The packing in the tower body is the basic component of gas-liquid two-phase contact. After the gas outside the tower body enters the tower body, the gas enters the packing layer. On the packing layer, there is spray liquid from the top and spray liquid in front, and a layer of liquid film is formed on the packing. When the gas flows through the packing gap, it contacts with the packing liquid film for absorption or comprehensive reaction, The packing layer can provide sufficient surface area without causing excessive resistance to the gas flow. The absorbed or integrated gas is collected by the demister and discharged out of the tower through the air outlet.